Prof. Tim W Simpson has a well earned reputation as a highly-cited authority in the field of Design for Additive Manufacturing (DfAM).
He has accrued over a decade of hands-on experience with nearly every AM technology at CIMP-3D, a part of The Pennsylvania State University where he is the Paul Morrow Professor of Engineering Design and Manufacturing.
For close to 25 years, he has educated both students and industry professionals on additive manufacturing design principles.
At the upcoming CDFAM Computational Design (+DfAM) Symposium, Prof. Simpson will discuss the correlated evolution of machines, materials, processes, software tools, and teaching methodologies over the past decade, with a particular emphasis on the transition from manual to computational design approaches.
Tim will delve into the differences in strategies for instructing fresh-eyed students as opposed to facilitating the ongoing development and upskilling of experience hardened engineers, addressing the unique learning requirements of each group.
Ahead of his presentation, we asked Prof. Simpson a few questions about his experience teaching DFAM.
We invite you to register for CDFAM, taking place in New York City on June 14-15, 2023, to hear his insights firsthand and engage with other experts in the DfAM field.
The additive manufacturing (AM) sector has evolved significantly over the past decade. Materials and processes have matured, moving from prototyping to production. Significant resources have been invested in developing new machines and materials, along with validating parts and processes. How has the methodology for teaching and applying Design for Additive Manufacturing (DFAM) evolved over this same time?
Design provides the important third leg of the stool that turns advances in materials and processes into functional parts when it comes to AM. So the design software and associated computational tools have evolved rapidly over the same period of time to keep up with the advances in materials and processes.
As the software and tools for design have evolved, people developed new ways to apply DFAM, which influenced how DFAM was taught–whether it is upskilling the current workforce (industry practitioners) or the future workforce (students) for successful careers in AM.
These two groups, however, have very different challenges when it comes to teaching DFAM.
The acronym is intentionally DFM in reverse since MFD limits the manufacturing processes a person considers during product design and development.
Fortunately, we have shown that this can be mitigated with AM training, workshops, and DFAM tools (e.g., worksheets), which helps shift their mindset to think “additively” vs. subtractively.
So the challenge lies in making them appreciate the cost and schedule pressures that they will face in industry along with understanding the realities of making functional, end-use parts with AM, not just plastic parts that can be easily 3D printed in most academic settings these days.
In both cases, teaching DFAM is all about unleashing one’s creativity. DFAM software and associated computational tools help spark one’s imagination, leading to innovative design solutions that are only possible with AM.
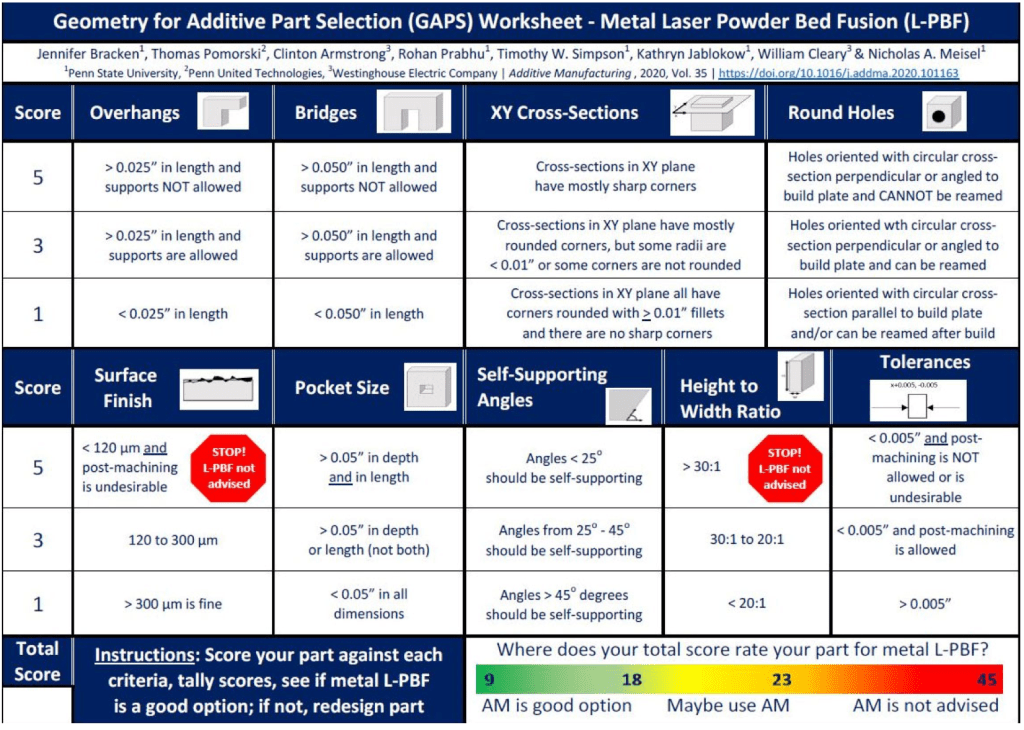
Have you seen a significant change in the approach that new students take to computational design tools over the same period as coding becomes more central to design and process development?
I think students are generally much more open to trying new software and computational design tools compared to most practitioners in industry.
Students also benefit from having the freedom and flexibility to “try and fail” on design projects and in the classroom, while industry practitioners are under the gun to deliver solutions on time, on schedule, with minimal risk. This often creates a risk-averse culture where people are afraid of failing, which limits their willingness to try new things. So, it’s not so much coding as it is having the freedom to fail combined with the time to learn from those failures.
As you now split your time equally between your role as System Design Innovator at NASA Langley Research Center and your position as the Paul Morrow Professor of Engineering Design and Manufacturing at Penn State University where you have been teaching and researching for over two decades, how do you view current the relationship between academia and industry, and how could the two sectors better communicate and help each other?
I think the two can learn a lot from each other, especially given the rapid pace at which AM technology and DFAM software tools are evolving.
As I said earlier, industry is often risk-averse (or too crunched for time) whereas students are much more willing to take risks (and have more time to do so); so, the more they can interact, the better.
I intentionally create these interactions several different ways. For instance, I use capstone design projects to pair senior engineering students with companies that want to dabble in AM. Industry-sponsored research becomes a way for students to apply AM to real-world projects while exposing industry to the latest and greatest DFAM tools and software. Student internships in industry are also important, and I even point companies to students working on hands-on projects like Formula SAE, Baja SAE, FIRST Robotics, etc. because those are the students that are not afraid to roll up their sleeves to make things work–and they are usually the ones pushing what our 3D printers can do.
So, it’s about finding synergies where costs, risks, and time pressures can align and become mutually beneficial.
This is why our Additive Manufacturing & Design (AMD) Graduate Program at Penn State has really flourished because it intentionally connects industry with academia on a level and in a learning environment where everyone benefits.
The resident students learn from the online industry practitioners and vice versa. Plus, the AMD faculty have a direct line to industry practitioners working in AM, which has also sorts of benefits for everyone involved. The phenomenal growth in the program (over 250 students from over 100 different companies have enrolled since it launched in 2017) is a clear sign of how well the two sectors can work together once good lines of communication have been established.
Along with your academic research and work at NASA, you also regularly write articles for a number of publications and your Think Outside The Journal to reach more people. How does the content of your writing differ for these audiences and what is a common message for both?
Great question as the different audiences certainly want to see, read, and learn different things.
Academics are pushing the limits of basic and applied research; so, they want to know all of the details about your work so that they can learn from it and differentiate their own work. For academic researchers, the methods are just as important, if not more so, than the results.
Industry, on the other hand, is looking for answers to real-world problems; so, they want to know the results first. If it worked and provided a benefit, then they will dig into the details and see how it can be applied in their situation. So when I write for industry, I start with the result and keep it as short as possible, which is very different from writing for a peer-reviewed publication.
Interestingly, learning what didn’t work is equally valuable because it saves people time and energy pursuing approaches that will not pan out.
Unfortunately, people aren’t as willing–or able–to share their failures, which is why I did the #AMWTF series on LinkedIn with Pete Zelinski at Additive Manufacturing Media. We intentionally shared several AM failures from my lab at Penn State, CIMP-3D, so that the rest of the community could learn from our mistakes. This definitely hit a nerve and was much more popular than either of us thought it would be.
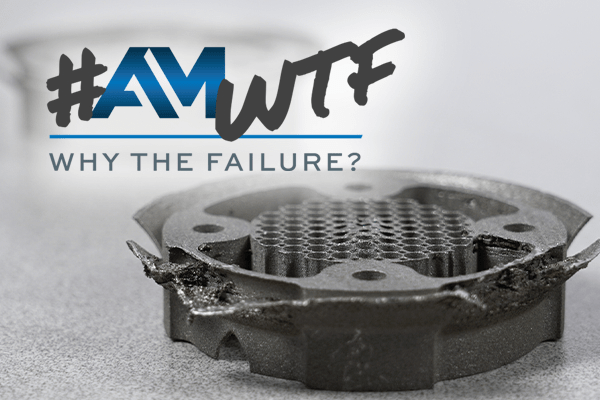
Aside from higher education, how else can we better prepare the design, engineering and manufacturing workforce for adoption of computational design tools at the individual, company and industry level?
This is where workshops, design competitions, projects, etc. help because they provide fun learning opportunities that don’t feel like training.
Such experiences can then be tailored for individuals, companies, or engage entire industries. GE’s bracket challenge on GrabCAD was a great example of this. It got nearly 700 responses from individuals all over the world, it helped solidify GE’s expertise with AM, and it provided a great example that continues to be used throughout the industry and in academic research.
What are the key points you hope to impart with your presentation at CDFAM and what do you hope to take away from the event?
Honestly, I’m really looking forward to learning about the latest computational tools for DFAM.
I always love seeing how people are combining the enormous computing power that is readily available with the latest breakthroughs in AI, generative design, bio-inspiration, etc. People’s creativity fascinates me, and I’m excited to see how it manifests in their tools.
As for my presentation, I’m planning a retrospective look at DFAM over the past decade.
We were fortunate to launch CIMP-3D right at the start of the hype cycle for metal AM, and I have seen several patterns over the years that I’ll share in my talk.
Some of those follow the 2-3 year research “cycle” that academics tend to fall into whereas other shifts are driven by start-ups, mergers, and acquisitions. CAD vendors have also taken very different approaches to keep up with the increasing demand for DFAM software and computational design tools. It will be very interesting to see how those capabilities compare to what others present at the event. I can’t wait!
To learn more about Tim’s decade of DfAM and more from over 30 experts in additive manufacturing, engineering and computational design register for CDFAM in NYC.