Matt Shomper on Computational DfAM & Biologically Inspired Engineering
Additive Orthopedics with Advanced Structures & Surfaces
Matt Shomper has been designing and manufacturing some of the most advanced Orthopedic implants using computational design and additive manufacturing drawing on inspiration from structures in nature and pure math. Whether it is the internal structure of the clubbing claw of the Mantis Shrimp, or custom tuned surfaces driven by Perlin noise algorithms, Matt’s applied research has been integrated into commercial products (and people’s bodies) around the world.
His work has helped leading companies in the medical space adopt additive manufacturing to help hundreds of thousands of people on the road to recovery.
Matt walks us through how he got started in computational DfAM, how nature inspires him, how math enables him to (attempt) to model the complex structures in nature, and how others can get started on their computational DfAM journey.
Q.
How did you get started in computational design and when did you first realize the potential of additive manufacturing in realizing the engineering requirements you were looking to fulfill?
A.
I had always been interested in the utilization of software to optimize design but was used to parametric tools driven by direct user inputs. I had dabbled with Grasshopper but it never really clicked in the specific design space I was in (orthopedic implants). Back in 2019, I was connected with the team at nTopology and was able to use their new software in alpha. It immediately resonated with me, and a new world of implicit design and new structures was opened up. It went deeper than just designing something “artistic” - now a lot of ideas tumbling around in my head for functional structures and medically-focused design features could be crafted in 3D space and actually produced!
Q.
In the past you have used algorithms to mimic the geometry of the structures of Mantis Shrimp’s claw, and a Bighorn Sheep’s skull (among others). How do you decide which bio-structures to examine and then replicate, and do you think we now have the software tools, materials and manufacturing capabilities to exceed the performance of structures created in nature?
A.
If there’s a cool image of a structure that exists on the internet (and I’ve seen), chances are I’ve attempted to replicate it! The stuff that I post is typically the stuff that works out, but other things (I’m looking at you diabolical ironclad beetle armor… 😒 ) are still in the works.
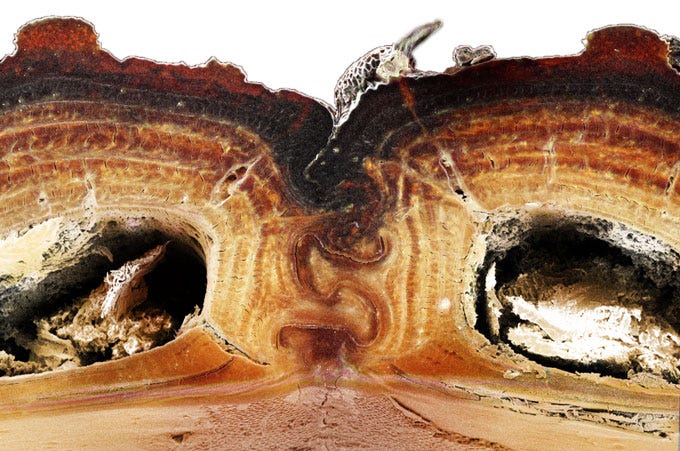
The things I’m most interested in are natural structures and textures, as they are directly applicable to osseointegrative features. I’m also interested in creating algorithms that push the envelope of software packages (think fractal tessellation) to try and mix the digital and organic.
I think we are getting very close to being able to replicate these structures’ properties with some of these new software tools that utilize computational design and implicit modeling. I also think we’re on the doorstep in the next year or two to using these softwares and advanced manufacturing to surpass what nature has given us, in some cases
Q.
Most of your current design work is focused on biologically advantageous spinal implants, how do these engineering problems transfer to other applications?
A.
My key focus areas are on structure types and textural (roughness) elements. Structures are directly applicable to a myriad of industries - aerospace, automotive, consumer products, etc.
Almost all advanced engineering problems are looking for ways to do more with less. And complex structures can help augment this regardless of the industry.
Textures for direct bone adhesion are applicable to heat transfer, textiles, lubricity, and more. I’ve been researching advanced texturing driven by complex fields, allowing for “directional” friction - an added benefit is that in the presence of ultrasonics they exhibit some really wild and interesting properties!
Q.
When assessing a particular engineering requirement and designing a solution, how much do you rely on simulation versus physical testing?
A.
When I was first beginning my professional engineering career in 2010, tools existed for mechanical structural simulation but there was a lot of suspicion of the results so we usually ended up performing mechanical testing. I think this had a lot to do with the risk of relying on simulation for medical devices, and the fact that the FDA eventually required mechanical testing to clear the product anyways.
As simulation tools have become more advanced, I find myself increasingly relying on at least an apples-to-apples comparison between variations, structure types, etc. I believe that it should now be directly ingrained in any good engineering toolset, specifically those in early-stage product development. Combined with additive manufacturing, it has the potential to dramatically reduce project phases prior to design freeze.
Q.
Given your expertise in design for additive manufacturing, potential clients must already have the perception that AM products will solve their problem when they engage with you. What is the process of ensuring that AM will be a suitable solution and how do you guide them through the realization of an application?
A.
This is a common occurrence - and it can be frustrating to be handed a complex problem with the expectation that a solution will manifest quickly and easily!
The single biggest problem is typically the customers lack of DfAM (design for additive manufacturing).
It’s easy to assume from the screen what you see is what you get (WYSIWYG), but how you produce parts has a huge bearing on the final product. I think people also expect an additive “expert” to instantly have a drag-and-drop solution that directly fixes their problem.
The thing is, I got so deep into this thing to solve problems with the technology that were unsolvable elsewhere - and these problems take time and iterations. So I first start with the ground rules of how a design on screen translates into parts in hand.
When customers have good expectations here, things tend to go more smoothly. Then, when they have a part in their hand that checks off the boxes down the path towards their solution, they typically light up and start to get excited about the next steps!
Q.
What are some common misconceptions companies have when they are investigating the adoption of additive manufacturing and how do you help them understand the constraints?
A.
WYSIWYG (mentioned above) - lack of understanding of process limitations
It’s FAST - why are my parts taking so long, lol
It’s EASY - everyone has a plastic printer nowadays so anyone can do it
As with many problems, the key is communication. We help them step through the difficulties in qualifying designs to the level the FDA is happy with. Most people have seen something like the below:
This is also true of additive manufacturing projects, especially in the heavily-regulated med device market. So if our customers are truly wanting to push the envelope of possibilities we make it clear that in our minds good is priority one… then they can choose between fast or cheap. : )
Q.
If someone is looking to advance their DfAM skills beyond ‘design for printability’, how would you advise them to extend their capabilities to really understand how to unlock the highest engineering performance and business value?
A.
For those really wanting to dive in deep, I’d recommend three softwares / pathways (all are free!):
Python project for open-source CAD design using implicit equations (FREP)
Software that can be used to generate the geometries of various types of lattices that are known as periodic cellular materials or architected materials - in particular, lattices based on triply periodic minimal surfaces.
Free and open source 3D creation suite
Why? It’s all about learning the base knowledge of how to fundamentally create these advanced concepts, and true expertise can draw upon multiple wells of experience. Working with open source or “homebrewed” creations helps the user better understand fundamental theories, and the troubleshooting aspects breed a more deep understanding.
The other thing I’d mention is that you gotta love math. Advanced additive structures and techniques go hand-in-hand with mathematical theory!
Q.
What are you exploring now in design for AM, and what are you most excited about learning about in the future?
A.
Right now I’m working on perlin and cellular noise-based structures to simulate organic bone. Pseudorandom noise is a really cool way to build structures from, and there’s not a lot of research that I could find.
Next up is some research on disconnected structures for a more structurally compliant implant design. It’s a continuation of the sinusoidal helical structure I worked on when I was studying mantis shrimp armor!
If your company is interested in exploring additive manufacturing to realize the design and production of an FDA approved medical advice, reach out to Matt and the team at Marle (nee Tangible Solutions) to discuss whether bio inspired additive manufactured Titanium components are the solution to your problem.
If you are interested in supporting articles such as this, consider becoming a paid subscriber of the DfAM Substack, or for free if you just want updates.
Related DfAM Articles: