Review of (some) DfAM Research Articles Reviewing DfAM Research Articles
In a previous article on the importance of DfAM education we touched on the academic research in the area. Following is a list of journal articles that explore the field of academic research into design for additive manufacturing, from the basics of design for manufacturability through lattice structure optimization and generative design.
This is in no way exhaustive and may lack academic rigor of a formal literature review but it is worth taking a snapshot of where we are today.
A bibliometric analysis of research in design for additive manufacturing
By Obi, Martins Ugonna; Pradel, Patrick; Sinclair, Matt; Bibb, Richard from the School of Design and Creative Arts, Loughborough University, Loughborough, UK
Purpose: The authors use a bibliometric approach to analyse publications from January 2010 to December 2020 to explore the subject areas, publication outlets, most active authors, geographical distribution of scholarly outputs, collaboration and co-citations at both institutional and geographical levels and outcomes from keywords analysis.
Findings reveal that most knowledge has been developed in DfAM methods, rules and guidelines. This may suggest that designers are trying to learn new ways of harnessing the freedom offered by AM. Furthermore, more knowledge is needed to understand how to tackle the inherent limitations of AM processes. Moreover, DfAM knowledge has thus far been developed mostly by authors in a small number of institutional and geographical clusters, potentially limiting diverse perspectives and synergies from international collaboration which are essential for global knowledge development, for improvement of the quality of DfAM research and for its wider dissemination.
The research process undertaken did seem to limit the amount of articles that met the selection criteria to only 349 articles including conference proceedings whereas a quick google scholar search for Design for Additive Manufacturing shows 4,380 results and DfAM “Additive Manufacturing” gave 4,180 results
Still the research correlates with much of the information available to researchers, students and engineers undertaking internal or external career development courses. While it is generally easier to codify and share design guidelines, going deeper into the functional performance and business decisions required for DfAM is much more difficult to synthesize into an easily digestible set of rules.
Their paper did see close to 30% of the articles cover the potential and performance of AM components vs restrictions and process which I am actually surprised the results were this high.
Design for additive manufacturing – a review of available design methods and software
By Anton Wiberg, Johan Persson, Johan Ölvander of Linkopings Universitet Tekniska Hogskolan, Linkoping, Sweden
Purpose – This paper aims to review recent research in design for additive manufacturing (DfAM), including additive manufacturing (AM) terminology, trends, methods, classification of DfAM methods and software. The focus is on the design engineer’s role in the DfAM process and includes which design methods and tools exist to aid the design process. This includes methods, guidelines and software to achieve design optimization and in further steps to increase the level of design automation for metal AM techniques. The research has a special interest in structural optimization and the coupling between topology optimization and AM.
Findings – Existing DfAM research has been divided into three main groups – component, part and process design – and based on the review of existing DfAM methods, a proposal for a DfAM process has been compiled. Design support suitable for use by design engineers is linked to each step in the compiled DfAM process. Finally, the review suggests a possible new DfAM process that allows a higher degree of design automation than today’s process. Furthermore, research areas that need to be further developed to achieve this framework are pointed out.
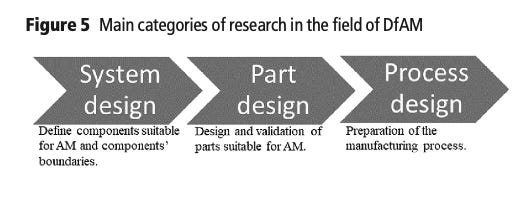
For their review of the DfAM landscape they break it down into three categories of system, part and process where I would argue that much of the existing research focuses toward the end of the part design and deep into the process design.
When they refer to Rodrigue and Rivette (2010) methodology where by if you are thinking of a system solution as an assembly of parts to be reduced or eliminated you are not really thinking of the engineering performance, but how to are going to modify your existing process for an additive process. This misses the point of DfAM needing a complete rethinking that they touch on later in the paper.
Another issue that is evident is the fast paced of technological development in software, materials and hardware in the three years since this paper was published reveals that some of the premises are no longer valid. This is in no way a criticism of the paper, simply something we need to take into account at the fast pace of software development.
In discussions on topology optimization there is mention of the need to manually reconstruct the top-op results into a CAD friendly BRep (boundary representation) for further design work and integration into larger CAD assemblies. This is no longer the case as most top-op producing software packages such as NX, Fusion 360, nTopology and Altair are all capable of automatically converting the top-op to BRep (to a certain complexity).
There is further discussion of process simulation and design automation, both of which have come a long way in both research and practice over the past few years. Specifically with computational design packages such as nTopology and Hyperganic allowing designers to programmatically engineer products and/or product variations.
It is impressive to see they took the system level DfAM to the next logical solution into automation of both the initial design and the final process.
Finally this incredibly comprehensive paper written by a supergroup of DfAM academics from a number of institutions around the world covers many aspects of opportunities, benefits and freedoms as well as the constraints.
Mary Kathryn Thompson, Giovanni Moroni, Thomas H.J. Vaneker, Georges M. Fadel, R. Ian Campbell, Ian Gibson, Alain Bernard, Joachim Schulz, Patricia Graf, Bhrigu Ahuja, Filomeno Martina
The development of DfAM knowledge, tools, rules, processes and methodologies has been cited as one of the technical principle challenges of AM. Insufficient understanding and application of DfAM is said to be limiting the overall penetration of AM in industry, holding back the use of AM for the production of end-use parts, preventing designers from fully benefitting from AM, and preventing AM from reaching its full potential in general. Once Design for Additive Manufacturing is well understood, that knowledge must be disseminated to current and future members of industry. Thus, AM-specific design education and design standards are also needed.
The paper goes on in detail to list many of the opportunities and benefits along with the design approaches required to realize those benefits. So much is covered in this one article I recommend anyone who is interested in a DfAM deep dive download and digest.
I was also hoping to review this paper but could not access and will update if I can get a copy.
Luis Lisandro Lopez Taborda, Heriberto Maury, Jovanny Pacheco of The Department of Mechanical Engineering, Universidad del Atlantico, Barranquilla, Colombia
Approach: This study analyzes the previous reviews (about 15 reviews) and based on the consensus and the classifications provided by these authors, a significant sample of research is analyzed in the design for additive manufacturing (DFAM) theme (approximately 80 articles until June of 2017 and approximately 280–300 articles until February of 2019) through descriptive statistics, to corroborate and deepen the findings of other researchers.
Findings: Throughout this work, this paper found statistics indicating that the main areas studied are: multiple objective optimizations, execution of the design, general DFAM and DFAM for functional performance. Among the main conclusions: there is a lack of innovation in the products developed with the methodologies, there is a lack of exhaustivity in the methodologies, there are few efforts to include environmental aspects in the methodologies, many of the methods include economic and cost evaluation, but are not very explicit and broad (sustainability evaluation), it is necessary to consider a greater variety of functions, among other conclusions
I would be interested to read why they believe there is a lack of innovation and whether they cover the results/performance of the designed components. I have reached out to the authors and will update as mentioned once I gain access.
Please reach out if there is particular research that you think I should share or if you are involved in any DfAM research and education.